A small price to pay to reduce uncertainty before investment
- Patrick Cloutier
- Aug 25, 2020
- 3 min read
A frozen food manufacturer wants to improve the productivity at one of its facilities which produces 20 different food products in different packaging formats for a total of 200 SKUs. These products are made, bagged and boxed on 11 processing lines each ending with a manual palletizing station. In some configurations, products are not boxed on the processing lines but left in bags and frozen in order to be later mixed and boxed as “combo packs” at an another production station.
The company is planning to invest millions of dollars in an extensive conveyor system to carry the cases of products from each of the processing lines to a central robotized palletizing area one floor below. When required, the system will also be able to bring bags of products from processing lines to the “combo pack” station.
All this material handling is currently being done manually by workers using pallet jacks and elevators. The goal of the project is to reduce labor costs by eliminating most of this material handling.
The equipment supplier has submitted a proposal in the form of conveyor drawings and specifications and the company wants to validate this proposal, to virtually test the conveyor system in full operation before going ahead with the proposed design. They chose 3D computer simulation for this purpose as it is the perfect tool for the job.
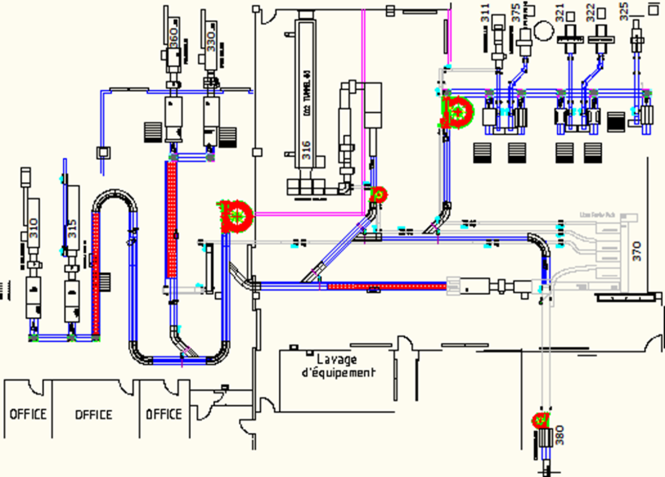
More specifically, the objective of the simulation is to help the company answer the following questions:
Can the proposed conveyor system satisfy the capacity requirements in terms of cases per hour?
If not, what needs to be changed? (Lengths, speeds, logic, line operating schedule, etc.)
Can the proposed robotized palletizing system satisfy required demand?
The major project steps are as follows:
Define “on paper” problem, objective, system, performance measures and alternatives to simulate. It’s an important step that saves time in the rest of the project.
Collect data: Processing line throughputs, products sizes, plant layout, proposed system design. This is the trickiest part as the simulation is only as good as the data used to create it. It is advisable to spend the right time to have the right information before starting to build the model.
Build simulation model. If steps 1 and 2 have been done correctly, this step is much faster especially with the ease of use of today’s simulation software.
Test, measure and adjust model. Even if we can’t truly validate the model of something that doesn’t yet exist, it is important to fully test it, measure results and adjust it so it behaves as close as possible the expected real system’s behavior.
Simulate alternatives and measure results. The following alternatives were simulated:
Scenario 1: No “combo packs”: 8 lines producing boxed products.
Scenario 2: With “combo packs”: 4 lines producing bagged products, 1 “combo pack” station boxing the 4 bagged products. 7 lines producing boxed products.
Scenario 3: Same as scenario 2 but with 4 bag lines synchronized (start-up times and speeds).
RESULTS
Simulation has answered the questions but with a few surprises:
The proposed conveyor system is not an issue and satisfies the required capacity.
For combo packs, synchronization of the lines was not an issue before because bags of products were produced in batches ahead and stored until needed to make combo packs. Now, to produce combo packs, feeding lines have to synchronize their start-ups and their speeds to supply the packing station efficiently. Otherwise products accumulate on conveyors for long periods and expire.
The palletizing system comprising of 2 robots will be the bottleneck of the new system and could cause major issues as the planned throughput will require them to operate near their fastest working cycle time. A manual overflow palletizing station has been added next to the robots and will be used in problematic periods.
The cost of this simulation study is a very small price to pay to reduce the uncertainty involved in this important investment.
Kommentare